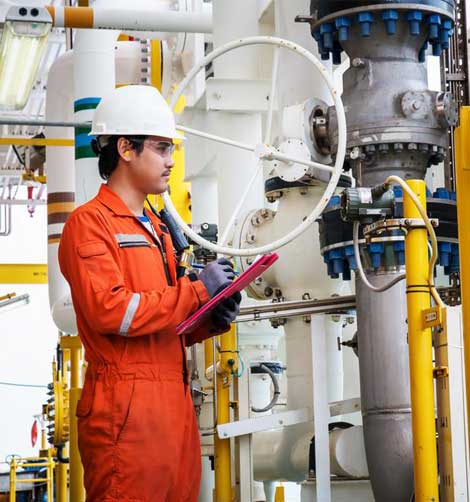
Non Destructive Evaluation (NDE) Inspection Methods and Techniques
NDE is used to describe measurements that are more quantitative in nature. Our methods would not only locate a defect, but would also be used to measure something about that defect such as its size, shape, and orientation. Our pocesses may also be used to determine material properties, such as fracture toughness, formability, and other physical characteristics. Here at Walzel we take pride in the techniques we use as well as the certification processes that we use to certify our technicians. On staff we have a Level III technician that trains, evaluates and monitors the NDE portion of our company. Below are descriptions of some of the techniques that we provide.Magnetic Particle Testing (MT)
This NDT method is accomplished by inducing a magnetic field in a ferromagnetic material and then dusting the surface with iron particles (either dry or suspended in liquid). Surface and near-surface flaws disrupt the flow of the magnetic field within the part and force some of the field to leak out at the surface. Iron particles are attracted and concentrated at sites of the magnetic flux leakages. This produces a visible indication of defect on the surface of the material. The images above demonstrate a component before and after inspection using dry magnetic particles.Ultrasonic Testing (UT)
In ultrasonic testing, high-frequency sound waves are transmitted into a material to detect imperfections or to locate changes in material properties. The most commonly used ultrasonic testing technique is pulse echo, whereby sound is introduced into a test object and reflections (echoes) from internal imperfections or the part’s geometrical surfaces are returned to a receiver.Penetrant Testing (PT)
With this testing method, the test object is coated with a solution that contains a visible or fluorescent dye. Excess solution is then removed from the surface of the object but is left in surface breaking defects. A developer is then applied to draw the penetrant out of the defects. With fluorescent dyes, ultraviolet light is used to make the bleedout fluoresce brightly, thus allowing imperfections to be readily seen. With visible dyes, a vivid color contrast between the penetrant and developer makes the bleedout easy to see. The red indications in the image represent a defect in this component.Positive Material Identification (PMI)
This method quickly and accuratly identifies the compisition of engineering alloys on location, on virtually any size or shape of material requested.Contact Us today to discuss the best NDE options available for your project including, Phassed Array, Visual Testing, Thickness Testing and much more.
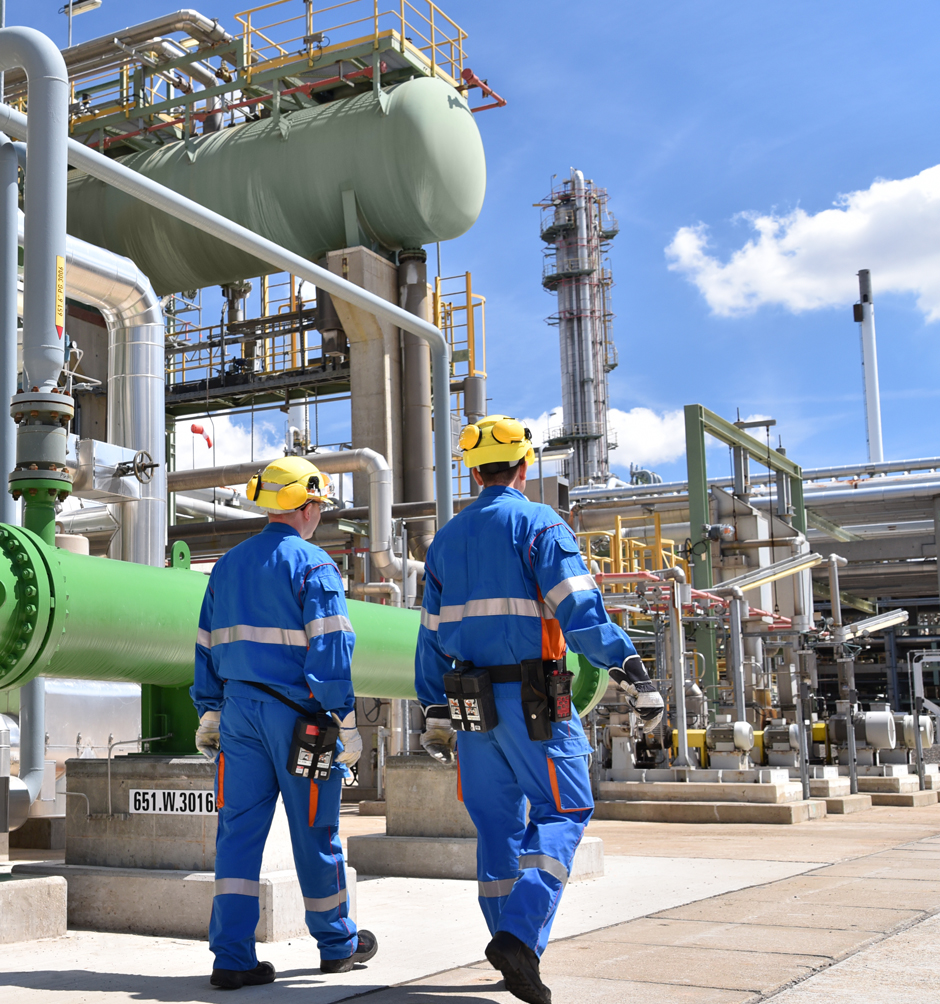
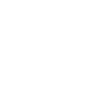